Chemical Vapor Synthesis (CVS)
A chemical vapor synthesis (CVS), as an aerosol process, has been used successfully to produce a wide range of the nanoparticles. In CVS the precursor materials are heated rapidly, and the vapors undergo chemical reactions such as thermal decomposition inside the reactor, leading to supersaturated vapor that will instantly undergo homogeneous nucleation and subsequent formation of particles.
a) metal particle production by chloride reduction
Metal chlorides reduce in the presence of hydrogen at high temperature to pure metal and hydrogen chloride as

where M denotes the metal e.g. cobalt and nickel. Similar reactions exist for other compounds, but for cobalt and nickel chloride the saturation vapour pressure of the chloride at the reaction temperature is high enough for particle production. The maximum mass concentration of particles available with the reduction method is limited by saturation vapour pressure of the metal chloride. The saturation vapour pressures of cobalt and nickel chlorides rise exponentially with temperature. The saturation vapour pressure of cobalt chloride is 13 kPa at 900°C, making the method stand out for the available mass concentration range. The evaporation rate of cobalt or nickel chloride from a crucible depends in addition to the saturation vapour pressure on the evaporation area and mass transfer limitations. Production rate of several hundred grams per hour has been achieved for e.g. Co, Ni and Zn nanoparticles.
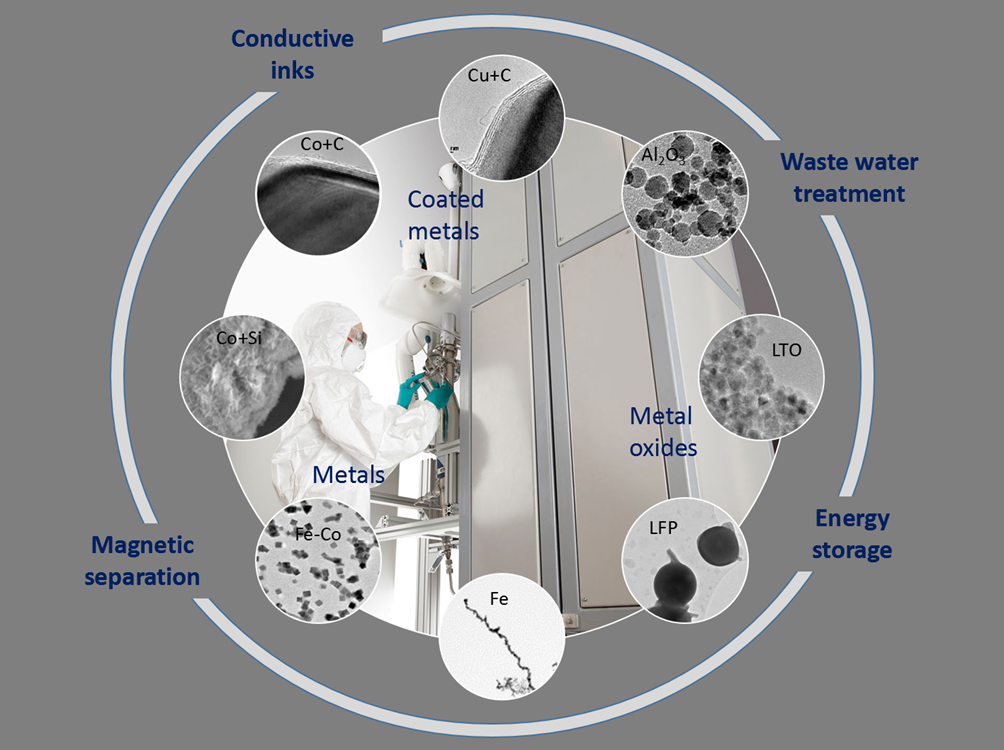
CAAR – Controlled Atmosphere Aerosol Reactor
b) porous tube reactor for magnetic particle synthesis (in collaboration with Venacontra Ltd.)
A porous tube reactor (PTR) method based on an atmospheric pressure chemical vapor synthesis method has been designed. The PTR method combines simultaneous reactions, particle formation and continuous dilution in a single-stage gas-phase process for nanoparticle synthesis. The aim is to achieve small primary particle size with a good production rate, fast and complete mixing of the gases, homogeneous conditions over the reactor volume to ensure fast gas phase reactions, a narrow size distribution of the particles produced, reduced wall deposition and fouling and pure synthesis products in the correct phase.
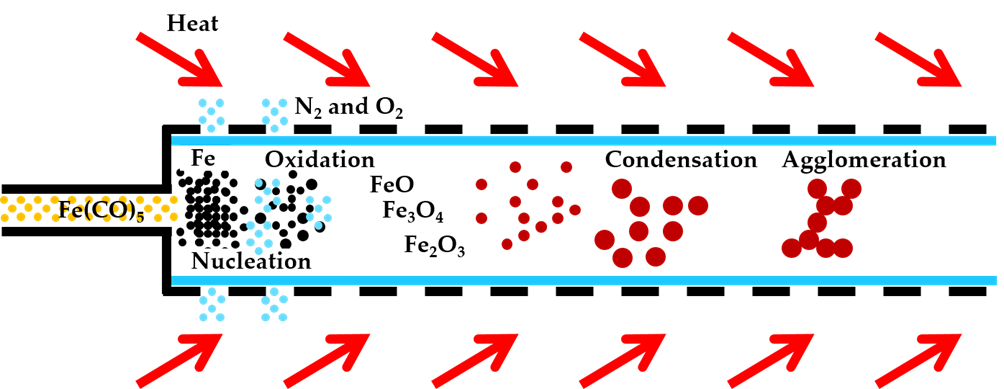